Zhengzhou Success Machinery Co.,ltd - Professional valve manufacturer
News Events
Latest News
The medium is mud. How should the valve be selected?
Release time:
Jun 25,2025
Mud often contains clay, sand, chemicals, and water, and has high viscosity, strong abrasiveness, and corrosiveness, which poses challenges for valve selection. The right valve can ensure smooth system operation, reduce maintenance costs, and extend equipment life. This article will analyse the impact of mud characteristics on valves, describe the appropriate valve types and selection criteria in detail, and help engineers and practitioners make accurate decisions.
The medium is mud. How should the valve be selected?
一、Mud characteristics
1、Physical properties: Viscosity is a key indicator of mud, influenced by solid phase content, particle size distribution, temperature, and chemical additives. High-viscosity mud has high flow resistance, which can cause valve operating torque to surge, making it difficult to open or close ordinary valves, and may even lead to jamming or damage; When mud containing sharp sand and gravel flows through valves, particles collide at high speeds with the sealing surfaces and internal valve components, acting like sandpaper and causing rapid wear on the seals. This significantly increases the risk of leakage, affecting system efficiency and environmental compliance.
2、Chemical properties: Depending on the operating conditions, the pH value of the mud fluctuates greatly. Acidic environments corrode metal valve materials, while alkaline conditions also erode some alloys. Some mud contains corrosive components such as chloride ions and sulphate ions, which accelerate metal corrosion, deteriorate valve strength and sealing performance, and threaten safe and stable operation.
二、Compatible valve types
1、Knife gate valve: Similar in structure to a gate valve, with a knife-shaped gate plate and a straight-travel opening and closing mechanism. The advantages include a full-bore design, ensuring smooth flow of slurry and minimal pressure loss; the knife plate efficiently cuts and blocks materials, making it highly adaptable to slurry containing fibres and large particles. However, sealing relies on the contact between the knife plate and the valve seat, which can be damaged by prolonged exposure to slurry erosion. It is advisable to select wear-resistant, corrosion-resistant elastic valve seat materials and perform regular maintenance or replacement.
2、Eccentric half-ball valve: The half-ball valve core rotates eccentrically to open and close the valve. When opening, the valve core moves away from the valve seat, reducing friction and wear. When closing, the eccentric design causes the ball crown to press tightly against the valve seat, ensuring a reliable seal that is resistant to slurry erosion and wear. This valve is widely used in high-pressure, high-concentration slurry systems. However, in complex operating conditions, the valve core and valve seat still require high-performance coatings or special alloy protection to ensure long-term sealing.
3、Ceramic ball valve: The valve core and seat are made of ceramic material, which has extremely high hardness, second only to diamond, and exceptional wear resistance, capable of withstanding long-term erosion by mud. It also has good chemical stability, resistance to acid and alkali corrosion, and stable performance at high temperatures. However, ceramic materials are highly brittle and prone to cracking under impact. Care must be taken to prevent collisions during installation and operation. They are suitable for mud pipelines with stable flow rates and no severe impacts. Selection must precisely match the pipe diameter and pressure to ensure safe operation.
4、Mud slurry pneumatic slurry valve
Featuring a sandwich-type structure and driven by a pneumatic actuator, this valve converts the energy of compressed air into mechanical energy via a cylinder to achieve linear motion for opening and closing. Examples include the PZ673H and X-10C models from Yongjia County Jucheng Valve Co., Ltd., which feature a compact design and small size.
It has good wear resistance and corrosion resistance, and is suitable for the transportation and control of various slurry media, such as pulp, sewage, coal slurry, etc. It has a wide range of diameters to meet different flow requirements, and has low pressure loss.
5、Mud gate valve Z973X-10
Structural Features: Electric drive, compact structure, high valve rigidity, smooth flow path, and low flow resistance coefficient. The valve seat sealing surface is made of hard alloy and polytetrafluoroethylene (PTFE), with soft graphite packing for reliable sealing and lightweight, flexible operation.
Performance Advantages: The valve body is available in carbon steel or stainless steel, suitable for various corrosive media. The fully open channel design prevents media deposition and blockage, while the U-shaped seal ring and elastic seal strip further ensure sealing performance.
6、ASCO Butterfly Valve
Structural Features: Simple structure consisting of a valve body, valve stem, butterfly disc, and seal ring. The butterfly disc is disc-shaped and rotates around the valve shaft to achieve opening/closing or regulation. Available in various structural forms, sealing configurations, connection types, and drive methods.
Performance Advantages: Suitable for controlling various fluids, including slurry, and capable of achieving good on/off control and flow regulation in low-pressure pipelines. The butterfly disc's movement has a scraping action, making it suitable for media containing suspended solid particles, with minimal flow resistance when open.
三、Key Considerations for Selection
1. Material Compatibility: The main body material is selected based on the corrosiveness of the slurry, with options including stainless steel (304, 316L, etc.), duplex steel, or special alloys; valve seats and seals use rubber (nitrile, fluororubber), polyurethane, or PTFE, balancing corrosion resistance, wear resistance, and flexibility to ensure sealing; valve cores and gate plates should be made of hardened metal or ceramic materials to enhance wear resistance, such as tungsten carbide-coated metal components or zirconia ceramic valve cores.
2. Valve diameter and pressure rating: The diameter is determined based on flow rate and velocity requirements. Larger diameters are selected for high flow rates to prevent excessive velocity from accelerating wear. The pressure rating must exceed the system's maximum operating pressure, with a safety margin to prevent overpressure leakage or damage. In complex operating conditions, industry standards and engineering experience should be referenced to appropriately upgrade the specifications.
Precise calculation of valve diameter and pressure rating: Determining the valve diameter is akin to planning the width of a river channel for mud flow. It must be precisely determined based on process flow requirements and velocity restrictions. Excessively high flow velocity increases the kinetic energy of mud particles, causing valve wear to rise exponentially; conversely, excessively low flow velocity may lead to solid phase deposition and pipeline blockage.
Based on empirical rules, maintaining a flow velocity of 1.5–3 m/s is optimal. From this, the appropriate pipe diameter can be calculated to ensure the mud flows smoothly in laminar or mild turbulent flow conditions. Pressure ratings are akin to dam heights; they must exceed the system's peak pressure and include a 20%–30% safety margin to prevent sudden high-pressure surges such as pressure pulses or water hammer impacts. The catastrophic scenario of high-pressure mud suddenly bursting through the valve must never occur, as it would mark the beginning of a production accident.
keywords
Previous Page:
:Next Page
Previous Page:
Next Page:
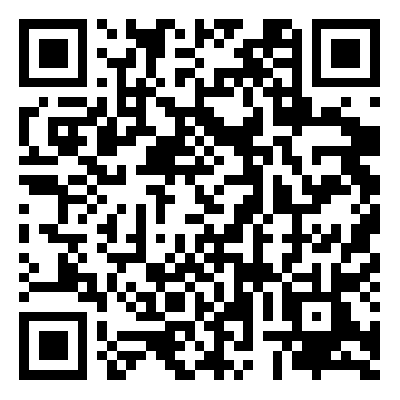
Follow Us
Zhengzhou Success Machinery Co.,ltd
TEL:+8618595868771
E-mail:sales@successmach.com
Address:98-1 Dengfeng Road, Shangjie District, Zhengzhou City, Henan Province