Zhengzhou Success Machinery Co.,ltd - Professional valve manufacturer
How to debug the electric knife gate valve after installation?
Release time:
Apr 28,2025
After the installation of electric knife gate valve, It can be debugged from the electrical connection check, valve manual debugging, electric control debugging, sealing performance test, etc., in order to ensure that it can operate normally, the specific steps are as follows:
1、Check the electrical connection to first confirm the power supply voltage and the rated voltage of the electric knife gate valve is the same, to see whether the specifications of the wire and cable meet the requirements. Then check whether the wiring is correct, whether the terminals are firm, whether there is any loosening, shedding phenomenon, to ensure that the earth wire is connected reliably, to prevent the risk of leakage.
2、Manual debugging before turning on the power supply, manually turn the handwheel of the valve, check whether the valve is flexible in opening and closing, whether there is any jamming, blocking phenomenon. At the same time, observe whether the movement of the valve plate is smooth, and confirm that the valve plate can be completely opened and closed, and the opening and closing position is consistent with the indication of the direction of rotation of the handwheel.
3、Electric control regulator pilot test:
(1)Turn on the power, carry out point operation, check whether the motor steering of the electric knife gate valve is correct. If the motor steering is wrong, it will lead to the valve opening and closing action contrary to the control signal, at this time need to adjust the motor wiring phase sequence.
(2)Stroke setting: Through electric operation, open the valve completely, adjust the open stroke limit switch to make it act accurately when the valve plate is completely open, and cut off the power supply of the motor. Similarly, the valve will be completely closed.
(3)Set off the travel limit switch to ensure that the valve plate is closed in place to stop the motor operation, in order to prevent damage to the valve over-opening and closing. Opening degree calibration: using the control system to give different opening degree instructions, such as 25%, 50%, 75%, 100%, etc., to observe whether the actual opening degree of the valve and the instruction opening degree is consistent. If there is a deviation, you can adjust the relevant parameters in the valve controller for calibration to ensure that the valve can accurately control the opening as required.
(4) Remote control test: send on/off valve and opening degree adjustment commands in the remote control terminal, check whether the valve can respond, and at the same time observe whether the valve status feedback signal can be accurately transmitted to the remote control terminal to ensure that the remote control function is normal.
4.Sealing performance test
It can be based on the valve use scenarios and media, choose the appropriate seal test method. For general conditions, can be hydraulic test, the valve will be closed, to the valve upstream pipeline injection of a certain pressure of water, keep the specified time, observe the valve plate sealing surface, valve body connections and other parts of the leakage phenomenon. If used for gas media, you can use the air pressure test or airtightness test, by detecting the pressure drop or applying soapy water to check the bubbles to determine whether the sealing performance is good.
5.Running noise and vibration check
In the valve electric operation process, pay attention to listening to the valve and motor with or without abnormal noise, observe the valve as a whole with or without obvious vibration. If there is anomaly, may be improper installation of the valve, internal components loose or motor failure and other reasons, need to be promptly investigated and dealt with.
keywords
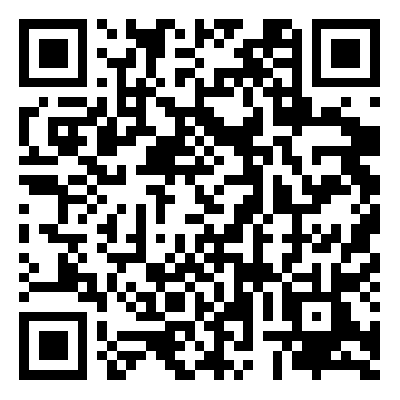
Follow Us
Zhengzhou Success Machinery Co.,ltd
TEL:+8618595868771
E-mail:sales@successmach.com
Address:98-1 Dengfeng Road, Shangjie District, Zhengzhou City, Henan Province